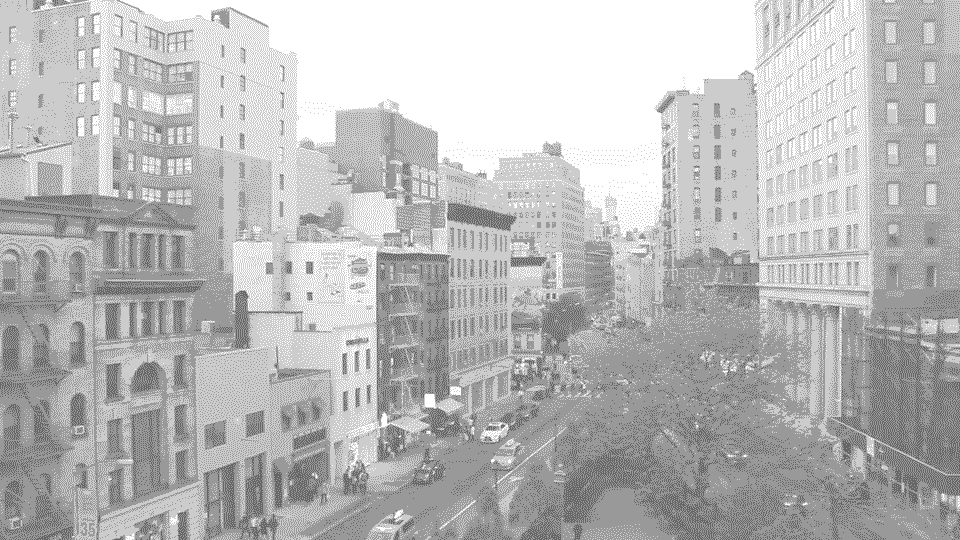
Stay tuned, we’ll be back…
We’re working on a complete overhaul of the website. Increasing resources and improving the experience for you.
In immediate need of an article you previously referenced? Reach out to archoverflow[at]gmail[dot]com. We’ll see if we can get you sorted asap.